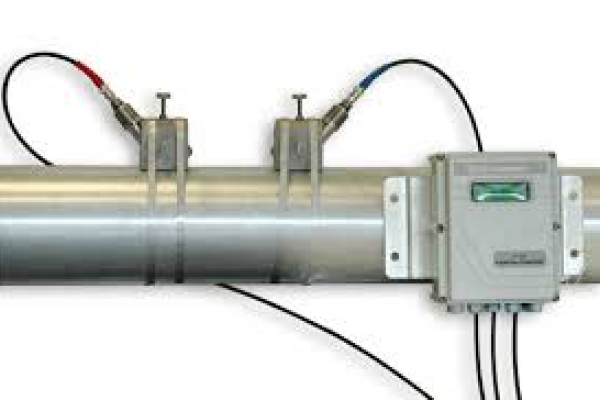
Non Destructive Testing
Nondestructive testing (NDT) is a wide group of analysis techniques used in science and technology industry to evaluate the properties of a material, component or system without causing damage. Below are some examples:
- Ultrasonic Flow Measurement
- Ultrasonic Thickness Measurement
- Ultrasonic Flaw & Crack Detection
Ultrasonic Flow Measurement
An ultrasonic flow meter is a type of flow meter that measures the velocity of a fluid with ultrasound to calculate volume flow. Using ultrasonic transducers, the flow meter can measure the average velocity along the path of an emitted beam of ultrasound, by averaging the difference in measured transit time between the pulses of ultrasound propagating into and against the direction of the flow or by measuring the frequency shift from the Doppler effect. Ultrasonic flow meters are affected by the acoustic properties of the fluid and can be impacted by temperature, density, viscosity and suspended particulates depending on the exact flow meter. They vary greatly in purchase price but are often inexpensive to use and maintain because they do not use moving parts, unlike mechanical flow meters. (definition from Wikipedia)
Ultrasonic Thickness Measurement
In the field of industrial ultrasonic testing, ultrasonic thickness measurement (UTM) is a method of performing non-destructive measurement (gauging) of the local thickness of a solid element (typically made of metal, if using ultrasound testing for industrial purposes) based on the time taken by the ultrasound wave to return to the surface. This type of measurement is typically performed with an ultrasonic thickness gauge. (definition from Wikipedia)
Ultrasonic Flaw and Crack Detection
Flaw detection is the most commonly used technique among all the applications of industrial ultrasonic testing. Generally, sound waves of high frequency are reflected from flaws and generate clear echo patterns. Portable instruments record and display these echo patterns. (definition from Azom.com)